Wilsonart® HPL or Wilsonart TFL
WHICH SURFACE IS BEST FOR YOUR PROJECT?
Discover Wilsonart High Pressure Laminate (HPL) and Thermally Fused Laminate (TFL) — two engineered solutions with key differences. Learn how to find the right surface for your performance, design, and budget requirements.
Find the right surface.
Choosing between Wilsonart HPL and Wilsonart TFL is easy. Simply identify your project priorities and get started with the chart below.








A higher premium.
Typically 30% lower than HPL.
Sheets can be shaped around contoured surfaces.
Flat panels. No postforming.
Choose Wilsonart HPL if your project…
- features high-traffic areas like countertops or reception desks
- needs aesthetic variety and high-end design
- requires high performance and longevity
- requires material to be contoured or postformed
Choose Wilsonart TFL if your project…
- needs a cost-effective solution for vertical and flat surfaces like cabinetry, wall paneling, and shelving
- includes decorative applications with low wear or impact
- prioritizes cost considerations
Compare surface applications.
Get the most out of every horizontal and vertical surface. Wilsonart HPL and TFL are uniquely engineered for specific applications.
















Meet Wilsonart HPL.
Wilsonart HPL is the premium choice for innovative engineering, long-term beauty, and a stunning range of designs. The material is created by layering specialty sheets under high heat and pressure, and bonding these layers to a durable substrate.


DURABLE MELAMINE OVERLAY LAYER


INNOVATIVE DESIGN LAYER


RECYCLED KRAFT PAPER LAYERS
Meet Wilsonart TFL.
Wilsonart TFL is the ultra-practical solution for budget-friendly applications that won’t experience high wear or high traffic. Creating the material is more simple than Wilsonart HPL, only requiring a decorative paper layer that is fused to a substrate using heat and pressure.


MELAMINE DESIGN LAYER


SUBSTRATE LAYER (PARTICLEBOARD OR MDF)


MELAMINE DESIGN LAYER
Discover best-matched coordination.
Can’t decide between Wilsonart HPL and Wilsonart TFL? Don’t worry — you can have both! Wilsonart Coordinated Surfaces gives you the power of industry-leading visual coordination with best-matched designs from Wilsonart HPL, Wilsonart TFL, and Edgebanding.
The right surface for your project.
No matter which surface you choose, both Wilsonart HPL and Wilsonart TFL are ready for projects of any scale.
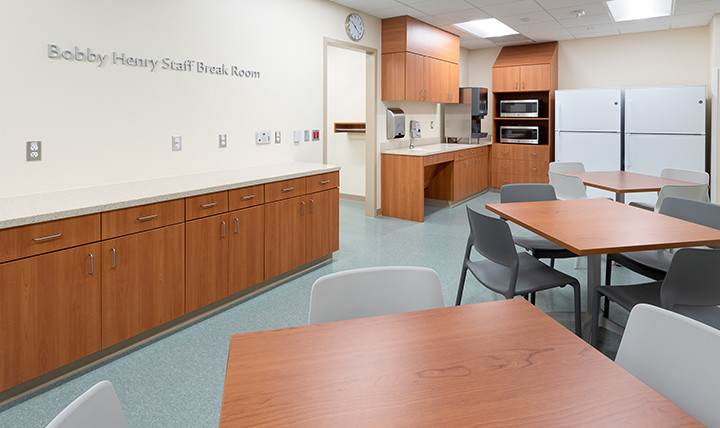
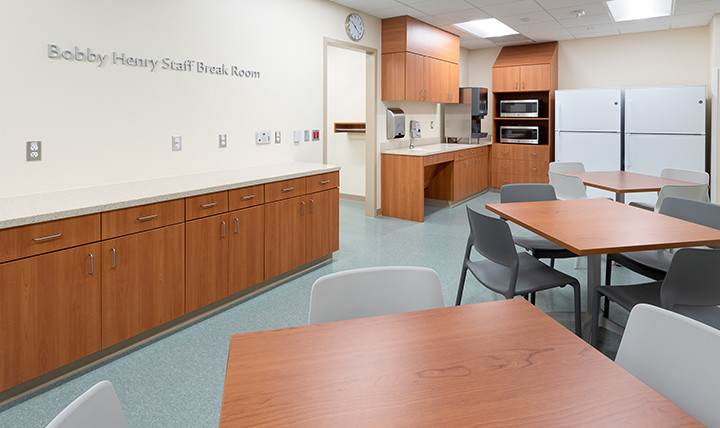
Healthcare
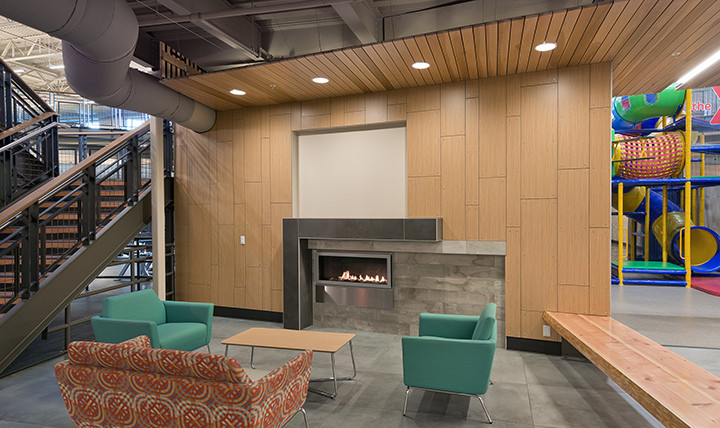
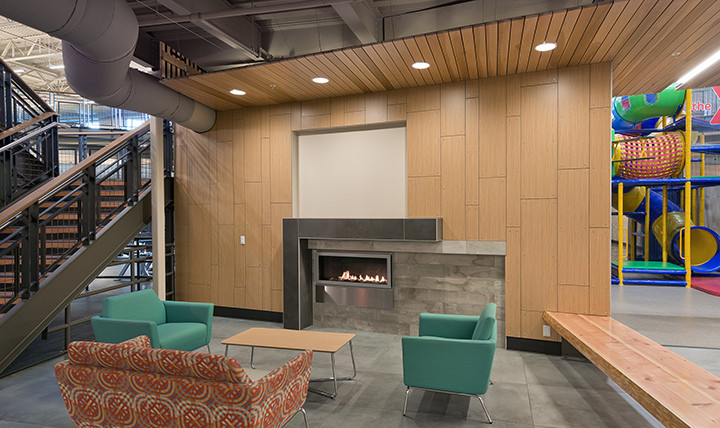
Hospitality
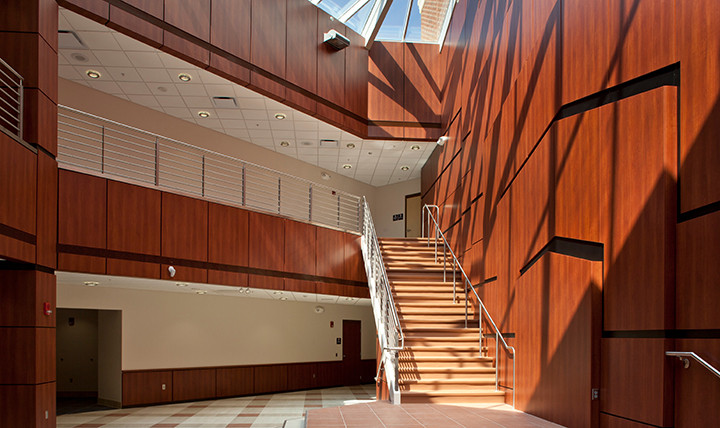
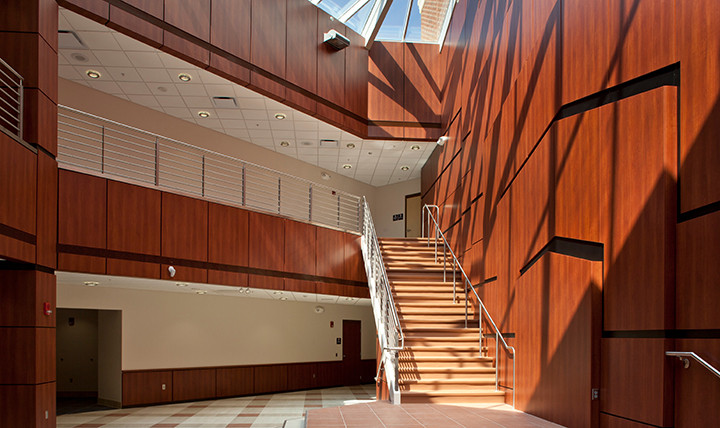
Education
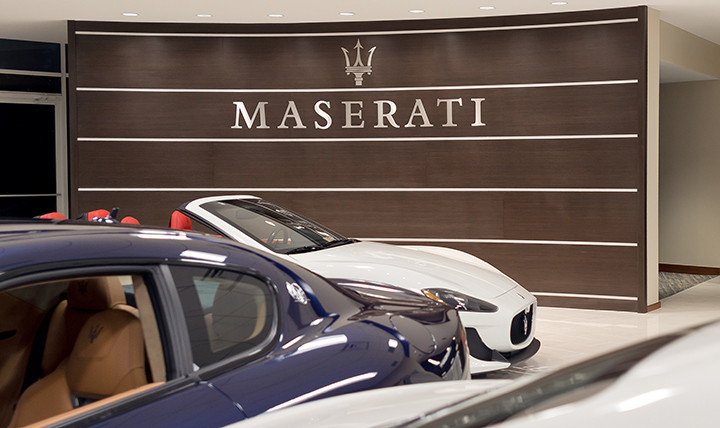
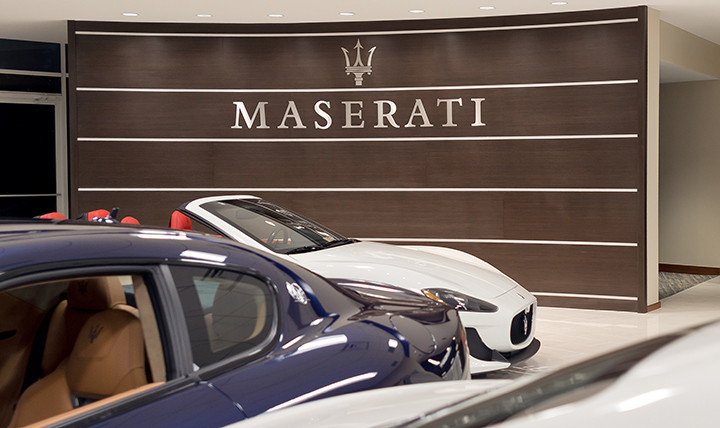
Retail
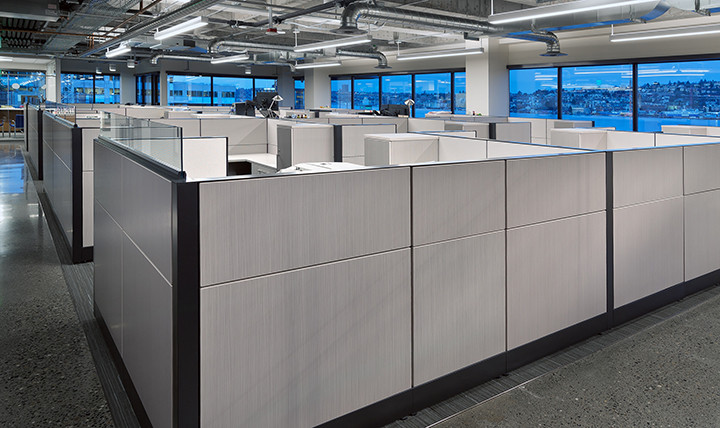
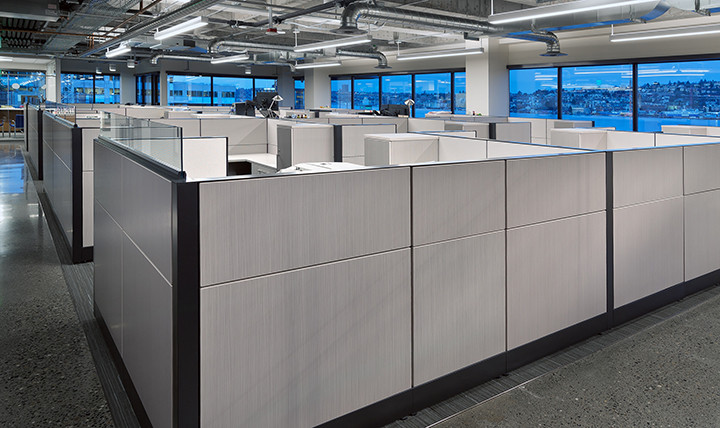
Workplaces
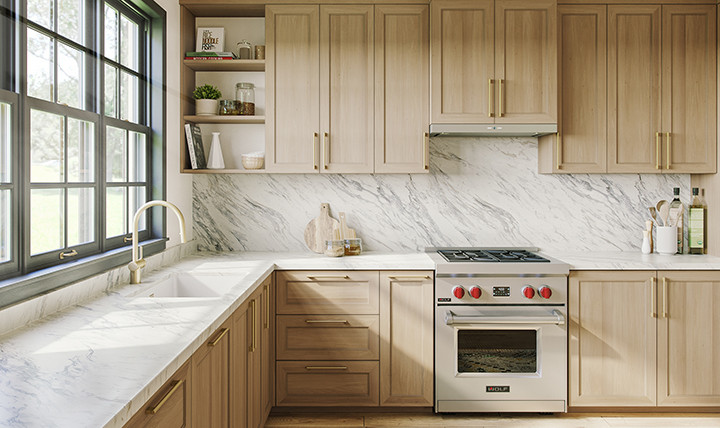
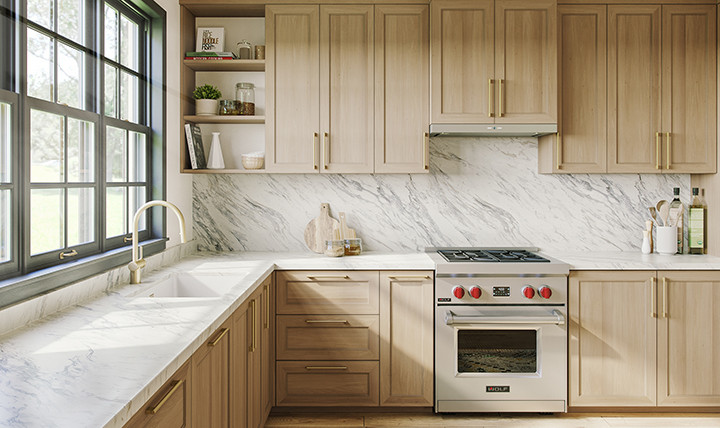
Residential
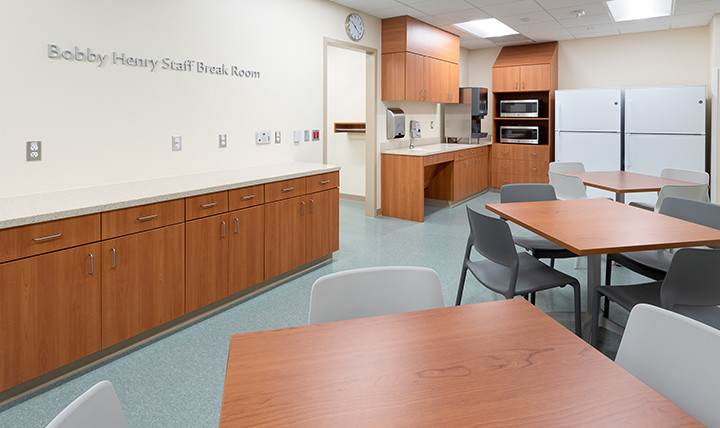
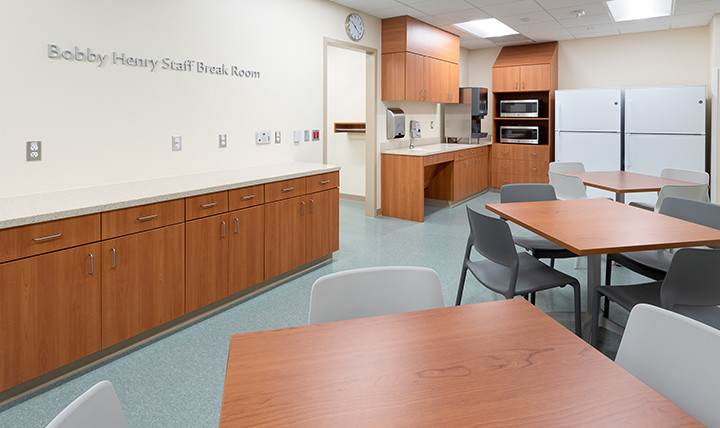
Healthcare
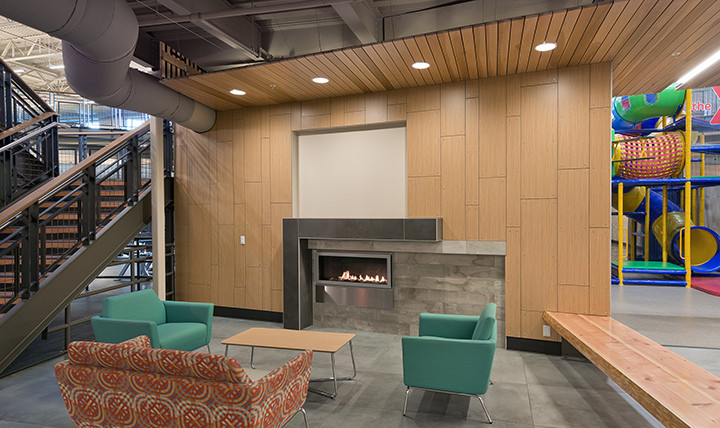
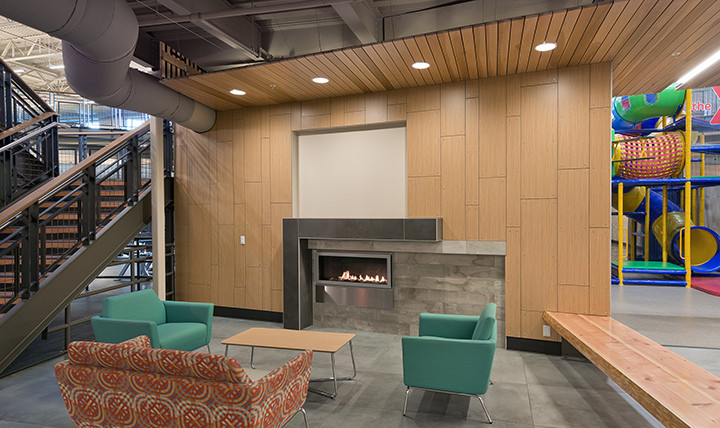
Hospitality
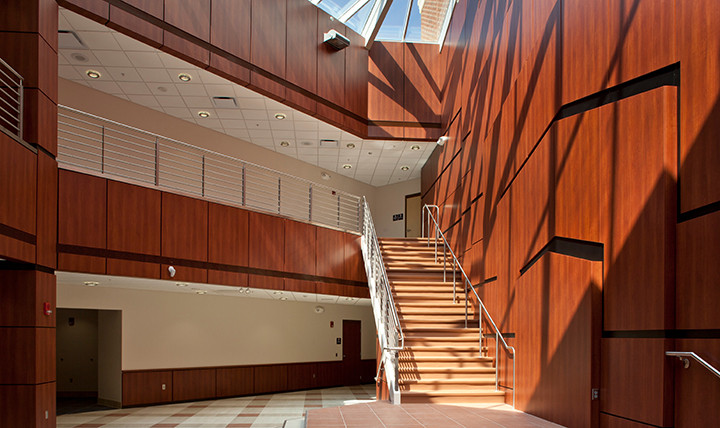
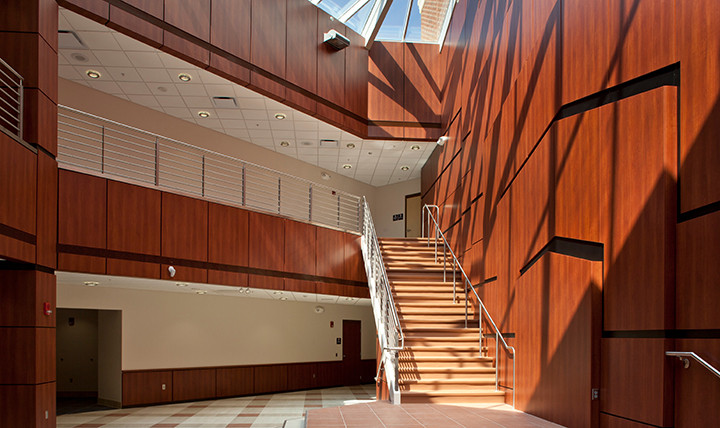
Education
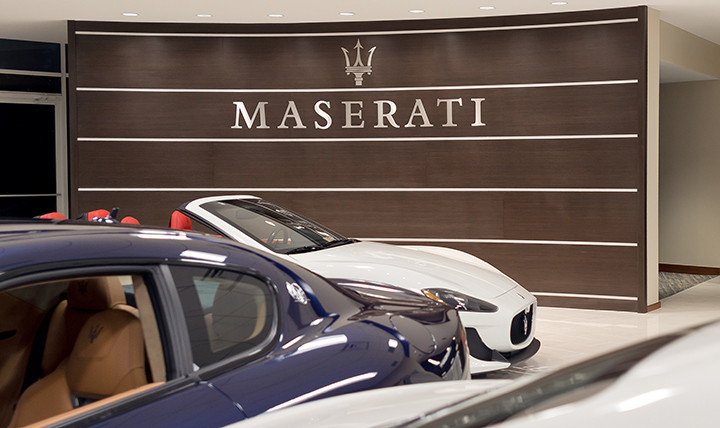
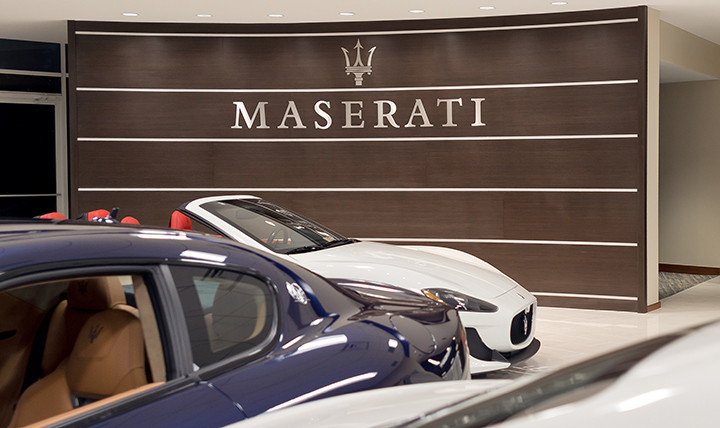
Retail
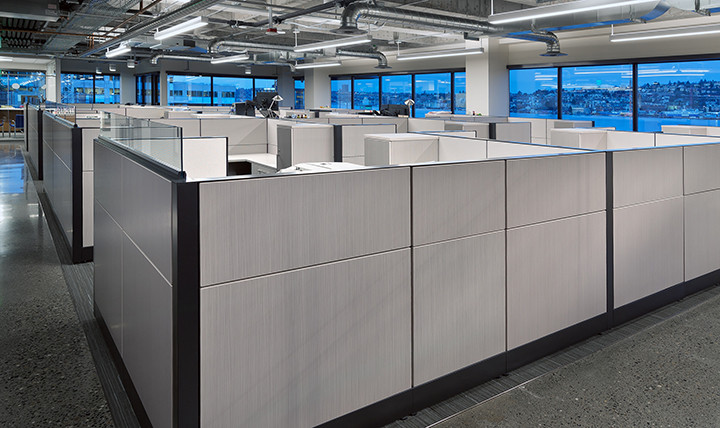
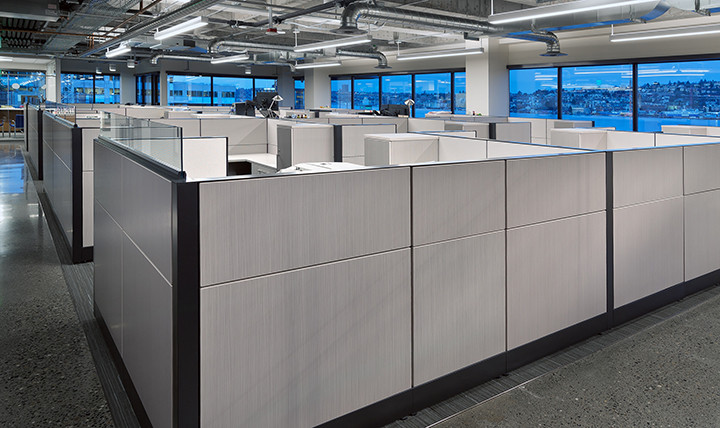
Workplaces
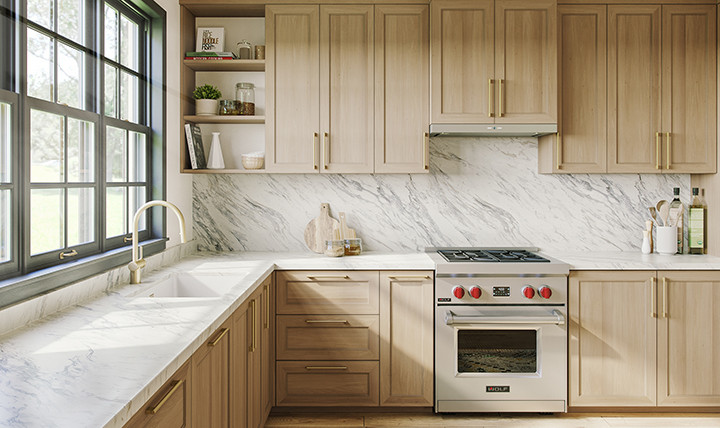
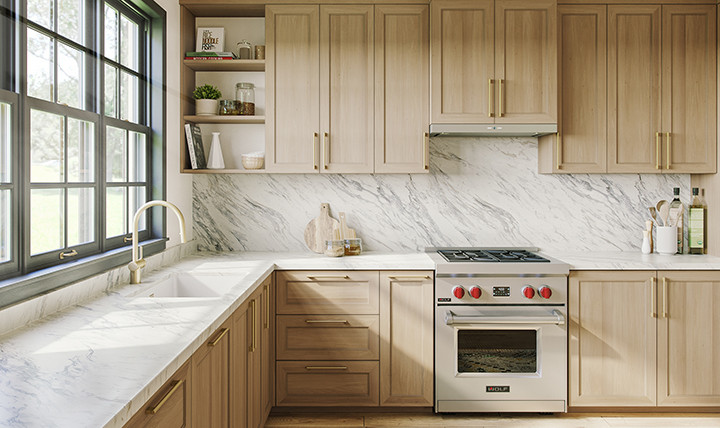
Residential
Let’s talk HPL and TFL.
Preparing for a project? Ready to specify a design? Our experts are ready to help.
Frequently asked questions
What is Coordinated Surfaces?
Wilsonart’s innovative coordinated surfaces program allows for a harmonious blend of HPL and TFL in a single application. This means you can maximize the durability of HPL on horizontal surfaces while maintaining a consistent design aesthetic by incorporating TFL for interior cabinet components and vertical applications. This strategic pairing showcases the versatility and adaptability of these laminate materials, ensuring they meet the specific demands of various applications.
Is there a minimum order for HPL or TFL?
There is no minimum order requirement for in-stock Wilsonart® HPL surfaces. However, Wilsonart® TFL requires an order minimum of 50 panels. All TFL is available On Demand.
What are the differences between HPL and MDF?
MDF (Medium Density Fiberboard) is a substrate material, while HPL (High Pressure Laminate) is a surface material. MDF is an engineered wood product made from compressed wood fibers and resin, and on its own typically looks unfinished. HPL is a high performing decorative sheet that can mimic the beauty of natural stone, finished woodgrains, fabrics, and more. HPL is preferred for surfaces like countertops and wall panels, valued for its durability and customizable designs.
How is HPL manufactured?
High Pressure Laminate (HPL) is made through a multi-step process. It begins with layers of kraft paper and phenolic resins, which give HPL its impact resistance and flexibility. The decorative paper is treated with melamine resins which adds durability, cleanability, and aesthetics. The layers are then pressed together under high heat, around 300°F, and pressure exceeding 1000 psi, creating a strong bond. The result is a robust, durable, and visually appealing material that’s used in countertops, doors, wall panels, furniture, and much more. Multiple finish options are available to give patterns realistic appearances.
How is TFL manufactured?
Thermally Fused Laminate, sometimes called melamine or melamine board, can be manufactured with enhanced visual and performance characteristics. TFL is made by fusing a resin-impregnated sheet of décor paper directly to a substrate such as particleboard or MDF. Heat and pressure activate the resin in the saturated TFL sheet, creating a permanent bond with the substrate. Surface textures created by stainless steel press plates emboss the decorative overlay to heighten the realism of woodgrain designs or control the gloss level of the surface from luxury matte, linear, and deep three-dimensional textures that are ultra-premium and on-trend.
What substrates are available to meet your TFL application requirements?
TFL panels come in various sizes, between 4'x8' and 5'x8', and are available with a range of substrates, including particleboard, MDF, NAF/ULEF, moisture-resistant, and fire-rated. Wilsonart® TFL may also be specified as FSC® certified.
Substrates | Benefits | Intended Use |
---|---|---|
Particleboard | An economical choice – costing around 10% less than MDF. Lighter and easier to handle than MDF and creates less dust when cutting than MDF. | Particleboard is a waste-wood product that's made by mixing sawdust with adhesives. Although it won't bow or warp like plywood, it can swell and become unstable when exposed to water. Suitable for furniture, underlayment, and as substrate for HPL countertops. |
Medium-Density Fiberboard (MDF) | MDF is designed to be used as a substrate for decorative finishes such as melamine and laminate. Edges machine well for planing, drilling, and routing. Has longer screw holding in both face and edge than PB. | Suitable for most joinery applications - interior cabinetry, wall and ceiling panels, and store fixtures. |
Moisture Resistance (MR) | MDF MR is specially formulated to offer enhanced moisture resistance. | MDF MR is designed to be used as a substrate for decorative finishes such as melamine and laminate. It is suitable for interior cabinetry, wall, and ceiling panels. |
Fire-Rated (FR) | MDF FR is a medium-density fiberboard specifically manufactured to include flame retardants. This dramatically improves the fire resistance and spread of flame qualities compared with standard MDF and most other timber–based panel products. | MDF FR is designed to be used as a substrate for decorative finishes such as melamine and laminate. It is suitable for interior cabinetry, wall, and ceiling panels. |
Low VOC (NAF) | Environmentally friendly choice. No-Added Formaldehyde (NAF). CARB-compliant. | Sustainable design. |
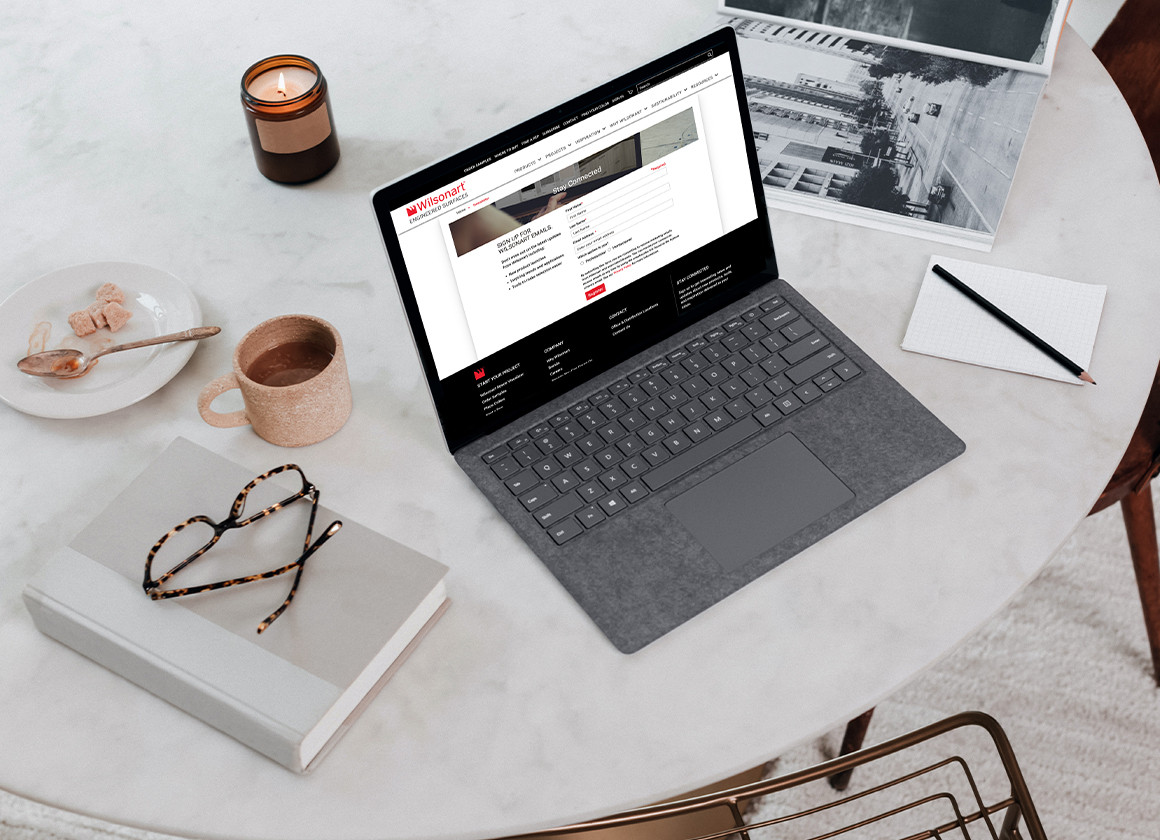
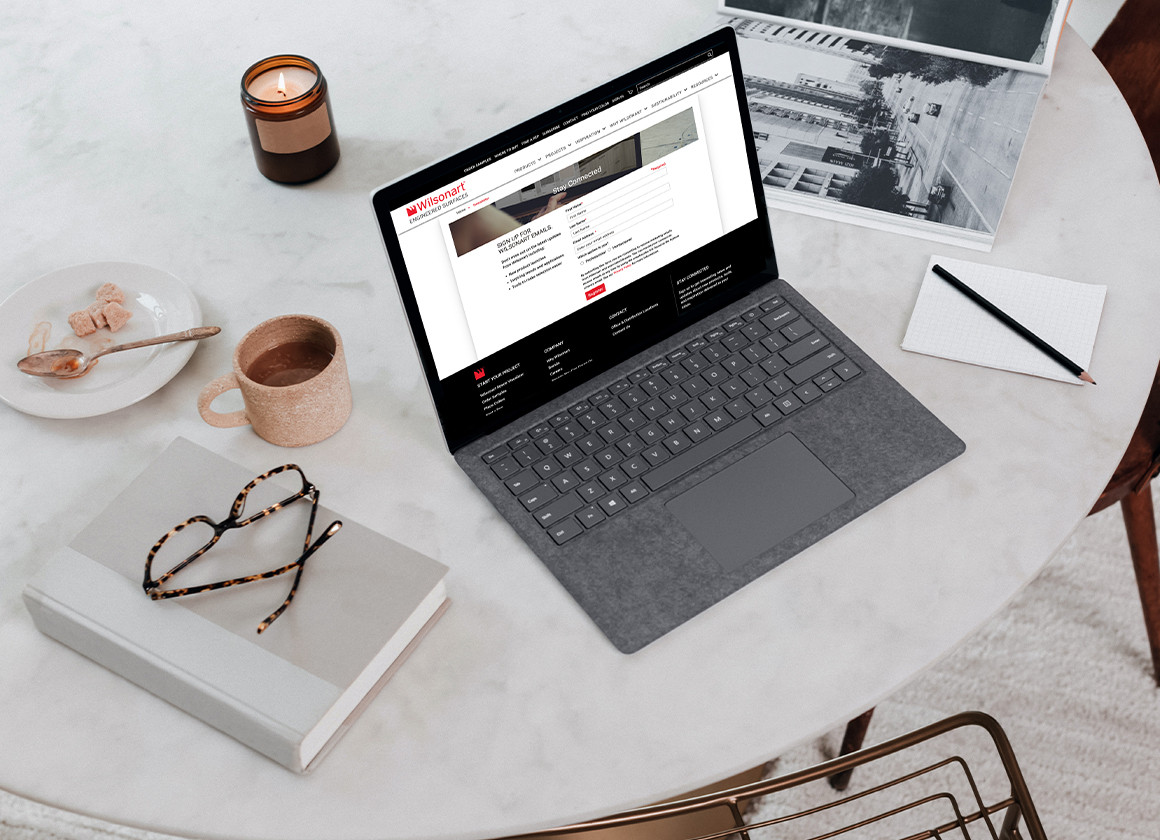
Get inspiration delivered
Sign up to get design inspiration, plus updates about new products and tools, delivered to your inbox.
Sign In
Register